.
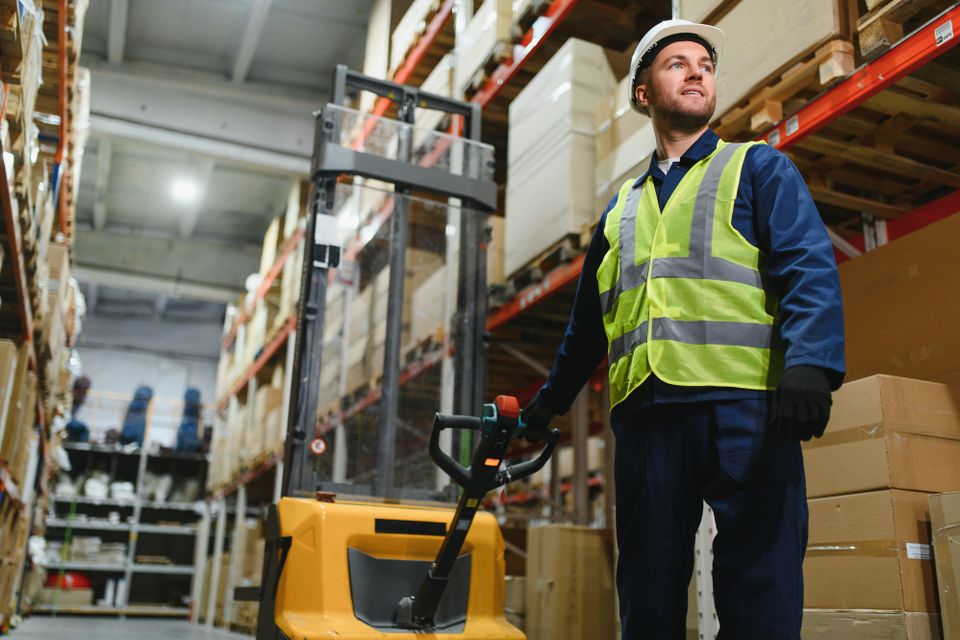
In any warehouse or industrial environment, the proper handling of materials is paramount to ensuring both product safety and worker well-being. Material handling doesn’t just refer to the physical movement of items; it encompasses a set of practices designed to reduce risks, ensure safe storage, and maintain smooth operations. This becomes especially important when working with storage systems like racks and shelves.
At JS Rack & Supply, we understand that correct handling of materials is not just about moving things from one place to another; it’s about creating a safe and organized system where products and workers are protected.
Let’s dive into the essential aspects of correct material handling as it pertains to storage systems and warehouses.
At JS Rack & Supply, we understand that correct handling of materials is not just about moving things from one place to another; it’s about creating a safe and organized system where products and workers are protected.
Let’s dive into the essential aspects of correct material handling as it pertains to storage systems and warehouses.