.
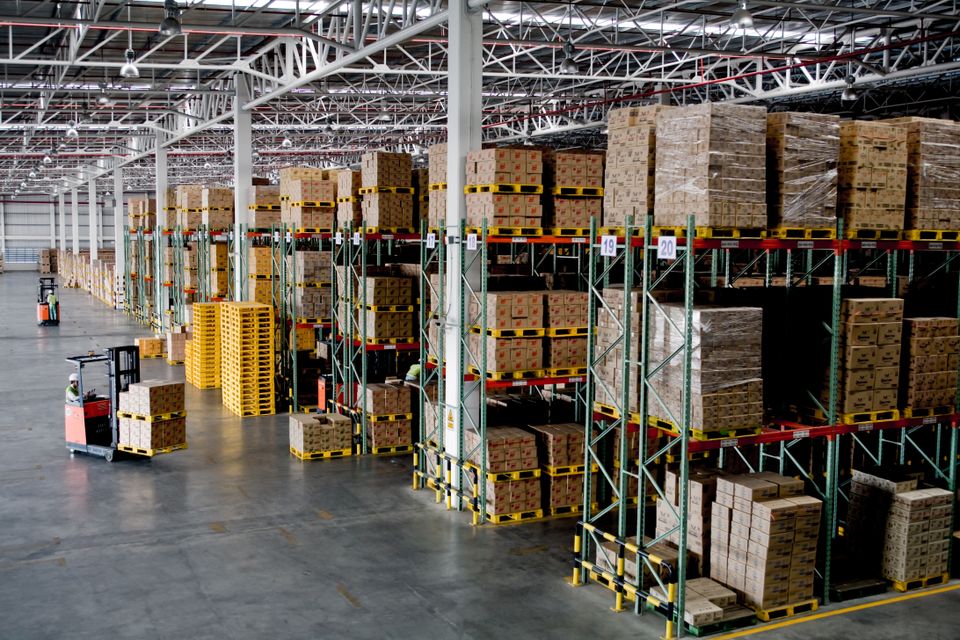
Considering a storage rack upgrade? If you're on the fence about investing in new or better storage solutions, there are a few key things to take into account that will help you decide on a course of action.
JS Rack & Supply is a national supplier of warehouse storage materials and tools based out of Estacada, OR. We have years of experience in helping customers to find the best storage racks and tools for them.
Five signs that your storage materials need to be replaced are -